What is CNC Controller? The CNC controller is an important part of CNC machine tools. It is the heart of any CNC machines system. A CNC controller connects all the important link between a computer system and the electrical components on the CNC machine such as the servo motors, spindle motor, coolant motor, lubrication motor and other electrical components. The main function of the CNC controller is to run the electrical components on the CNC machine tools to drive the mechanical parts on the CNC machine or to control the multiple axes on the machine.
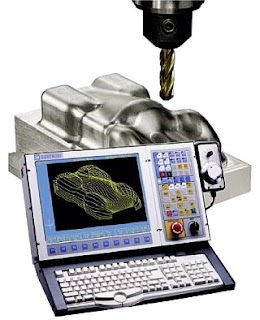
Centroid CNC Controller
Basically, to drive the mechanical components on the CNC machine, the CNC controller will work side by side with CPU unit, computer systems, servo motor drive, motion controller, PLC unit and inverter to form a sub-field of automation to determine the tool position on each axis, moving velocity of each axis, spindle speed and to run other electrical components such coolant pump, hydraulic pump, lubrication pump and light.
In fact, the powerful CNC controller does far more than drives the motors which some of the controllers have the capabilities to detect and control the limit switches, the coolant flow amount, air pressure, hydraulic pressure, detect temperature, detect and run up to 200 tool positions and more. CNC Controls enhance the machine's productivity capabilities with a new level of easy-to-access information and programming tools. Some of the CNC controller systems are available for a wide-range of applications such as grinding, drilling, digitizing, engraving, probing, cutting, milling, punching, turning and many more.
Nowadays, the modern CNC controllers range from professional stand alone system built-in with keyboard and user interface to hobby use CNC controllers that require a personal computer. The modern controllers come with CNC software packages such as Computer Aided Design (CAD) software, Computer Aided Manufacturing (CAM) software and the Computer Numerical Control software. The CAD is used for displaying and editing designs on the computer. The CAM is used to convert the geometry into tool paths or computer numerical codes called G codes that can be understood by the machine tools. The Computer Numerical Control software will control the machine tools to physically cut your 2D or 3D workpiece in real time.
Most of the CNC controllers in the market are provided with the user interface such as RS232 port, USB flash memory port and LAN port. It is easier to transfer the cnc programs and any files from computers or USB flash memory to CNC controller. LAN port can be connected to router or Hub to establish the connection between the controller and other computers. Using RS232 you can transfer or modify any files on controller from other PC or laptop.
Most of CNC Controllers are equipped with
* USB port to download and upload the files between controller and USB flash memory
* RS232 port to connect the controller with a personal computer (PC) or laptop
* LAN port to connect the controller with other computers
* Probe port to auto set the tool height offset and set tool reference point
* Axis buttons to control the movement of each axis on the machine
* MPG port
* Feedrate button to control the velocity of machine tools
* Speed control (FAST/SLOW) button when moving the axis
* Spindle adjustable speed button
* Spindle CW and CCW buttons
* Spindle ON/OFF button
* Auto and manual function buttons for spindle and coolant
* Coolant ON/OFF button
* Tool Check button
* Tool path viewer and cut-time estimation
* Single mode button to run the machine tool block by block program number
* Light ON/OFF button
* Incremental button 0.1, 0.01 and 0.001
* Start, stop, repeat on any line of G-code
* Emergency stop button
* and much more